Introduction: Taylorism Attempted to Use Scientific Principles to Better Handle Which Aspect of Business
Taylorism Attempted to Use Scientific Principles to Better Handle Which Aspect of Business, also known as Scientific Management, is a management theory that applies scientific principles to improve business operations. Developed by Frederick Winslow Taylor in the late 19th and early 20th centuries, Taylorism aimed to increase productivity, reduce waste, and optimize labor efficiency. Taylor’s ideas were revolutionary at the time, profoundly impacting industries worldwide.
The central question is: Which aspect of business did Taylorism aim to improve using scientific principles? The answer lies in workplace efficiency, labor productivity, and overall business operations management. Let’s explore this concept in detail and understand how Taylor’s methods transformed modern business practices.
Background: Who Was Frederick Winslow Taylor
- Frederick Winslow Taylor (1856-1915) was an American mechanical engineer and one of the first management consultants.
- He is known as the “Father of Scientific Management” for developing principles that applied scientific methods to labor management.
- Taylor’s work, particularly his book “The Principles of Scientific Management” (1911), became a foundational text in management theory.
The Core Aspect of Business Taylorism Focused On

The primary aspect of business that Taylorism aimed to handle using scientific principles was workplace efficiency and labor productivity management. Taylor believed that businesses could significantly increase productivity by scientifically analyzing tasks, standardizing workflows, and properly training workers.
Key Principles of Taylorism and Their Role in Business Efficiency
1. Time and Motion Studies
Taylor pioneered the use of time and motion studies to analyze how tasks were performed.
- What Are Time and Motion Studies?
- Time studies measure how long it takes to complete a task.
- Motion studies analyze the physical movements required to perform a task.
- Purpose: To identify and eliminate inefficient movements and reduce the time taken to complete tasks.
- Impact: Workers became more productive by following optimized methods.
Example: At the Bethlehem Steel Company, Taylor’s time and motion studies helped workers increase their daily output from 12.5 tons to 47 tons, leading to significant productivity gains.
2. Standardization of Work Processes
Taylor emphasized breaking down complex tasks into smaller, simpler actions and ensuring that each worker followed the best method.
- What Is Standardization?
- Establishing a single, best way to perform a task.
- Creating detailed procedures for every job function.
- Purpose: To ensure consistency, reduce errors, and increase efficiency.
- Impact: Workers performed tasks faster and with greater accuracy.
✅ Example: In automobile assembly lines, standardization led to faster production times and fewer mistakes.
3. Division of Labor and Specialization
Taylorism promoted dividing tasks into specialized roles, enabling workers to become experts in their assigned duties.
- What Is Division of Labor
- Assigning specific, repetitive tasks to individual workers.
- Purpose: To increase efficiency by enabling workers to perform tasks more quickly and with greater skill.
- Impact: Faster production and reduced labor costs.
✅ Example: Henry Ford’s assembly line, inspired by Taylorism, reduced the time to produce a car from 12 hours to 90 minutes.
4. Scientific Selection and Training of Workers
Taylor believed that businesses should hire workers based on their skills and train them using scientific methods.
- What Is Scientific Selection?
- Using tests and performance evaluations to hire the best candidates.
- Purpose: To match workers to tasks that suit their abilities.
- Impact: Reduced turnover, improved productivity, and better job performance.
✅ Example: Modern companies use aptitude tests and training programs inspired by Taylorism principles.
5. Incentive-Based Pay Systems
Taylor introduced the concept of piece-rate pay, where workers were paid based on their productivity.
- What Is Piece-Rate Pay?
- Workers earn wages according to the number of units they produce.
- Purpose: To motivate employees to work harder and faster.
- Impact: Increased productivity and reduced idle time.
✅ Example: In sales jobs, commissions based on performance are a direct application of Taylor’s incentive principles.
The Impact of Taylorism on Business Operations
1. Increased Productivity and Output
Taylorism’s focus on efficiency and standardization led to unprecedented gains in productivity.
- Efficient Workflows: Time and motion studies eliminated unnecessary movements.
- Specialization: Workers became experts in their tasks.
- Motivation: Incentive pay encouraged higher performance.
✅ Case Study: At the Ford Motor Company, assembly line production reduced manufacturing time for the Model T from 12 hours to 90 minutes, cutting costs and increasing production capacity.
2. Cost Reduction and Profit Maximization
By optimizing workflows and reducing waste, businesses significantly lowered their operating costs.
- Reduced Labor Costs: Division of labor minimized training time and enabled less-skilled workers to perform tasks.
- Lower Material Waste: Scientific methods minimized errors and material losses.
- Higher Output: Increased production capacity allowed businesses to meet higher demand.
3. Improved Quality Control

Standardized procedures ensured consistent output quality.
- Consistent Techniques: Workers followed uniform methods, reducing defects.
- Error Detection: Time and motion studies highlighted inefficiencies and mistakes.
- Training: Workers were skilled in standardized methods, ensuring quality.
4. Better Workforce Management
Taylorism introduced scientific methods for hiring, training, and evaluating employees.
- Scientific Hiring: Skills assessments ensured the right people were hired.
- Focused Training: Workers were trained in optimized methods.
- Performance Evaluation: Regular assessments ensured productivity standards were met.
Taylorism Influence on Modern Business Practices
1. Assembly Line Production
Henry Ford’s assembly line, a direct application of Taylor’s principles, revolutionized manufacturing.
- Mass Production: Enabled large-scale production of affordable goods.
- Lower Costs: Reduced labor costs through task specialization.
- Faster Production: Cut production times dramatically.
2. Lean Manufacturing and Six Sigma
Modern manufacturing methodologies like Lean Manufacturing and Six Sigma are rooted in Taylorism.
- Lean Manufacturing: Focuses on eliminating waste, inspired by time and motion studies.
- Six Sigma: Uses data to improve processes and reduce defects, similar to Taylor’s scientific methods.
3. Modern Management Techniques
Taylorism paved the way for modern management techniques:
- Performance Metrics: Businesses use KPIs (Key Performance Indicators) to measure efficiency.
- Task Automation: Machines now perform repetitive tasks more efficiently.
- Productivity Tools: Time-tracking software is a digital version of time and motion studies.
Criticisms of Taylorism: The Dark Side of Efficiency
1. Dehumanization of Workers
Taylorism was criticized for treating workers like machines.
- Monotonous Work: Repetitive tasks caused boredom and dissatisfaction.
- No Creativity: Workers had little opportunity to innovate.
- Physical Strain: High demands for productivity caused stress and exhaustion.
✅ Example: Workers on Ford’s assembly line faced high turnover rates due to monotonous tasks.
2. Worker-Management Conflicts
The focus on productivity often caused tension between workers and management.
- Exploitation Concerns: Workers felt pressured to produce more without fair pay increases.
- Labor Strikes: Conflicts over pay and working conditions led to strikes and protests.
3. Ignoring Human Motivation
Taylorism’s emphasis on financial incentives ignored other motivational factors.
- No Job Satisfaction: The focus on pay alone failed to address the need for personal growth.
- Low Morale: Workers felt undervalued and replaceable.
Modern Adaptations: Balancing Efficiency and Humanity
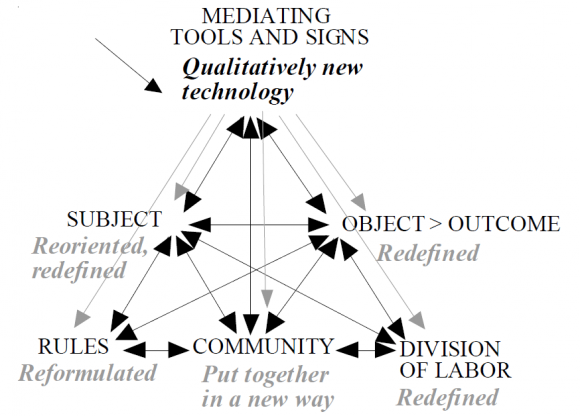
1. Human Relations Management
Management theories like Elton Mayo’s Human Relations Theory emerged in response to Taylorism.
- Focus on Employee Well-Being: Addressed workers’ social and emotional needs.
- Teamwork and Collaboration: Encouraged group participation and feedback.
- Employee Recognition: Emphasized the importance of appreciation and respect.
2. Total Quality Management (TQM)
TQM combines Taylorism’s efficiency with employee involvement.
- Continuous Improvement: Focuses on ongoing optimization of processes.
- Employee Involvement: Encourages workers to suggest improvements.
- Customer Focus: Prioritizes quality and customer satisfaction.
3. Agile Management Practices
In modern businesses, Agile Management promotes flexibility and collaboration.
- Adaptive Planning: Adjusts processes based on feedback.
- Collaboration: Teams work together to solve problems.
- Employee Empowerment: Encourages initiative and innovation.
Conclusion: The Legacy of Taylorism in Modern Business
Taylorism, through its scientific principles, sought to better handle the aspect of business related to workplace efficiency, productivity, and operations management. While it revolutionized industries by introducing methods like time studies, standardization, and incentive-based pay, it also sparked debates about worker treatment and job satisfaction.
Today, businesses continue to build on Taylor’s principles, blending efficiency with human-centered management approaches. The result is a modern business environment that values both productivity and employee well-being, demonstrating that the lessons of Taylorism are still relevant over a century later.
Disclaimer
This article on “Taylorism attempted to use scientific principles to better handle which aspect of business?” is for informational purposes only. It reflects research-based insights and does not constitute professional business advice. Readers should consult experts for tailored strategies suitable for their specific business needs.